Optimizing Undersea Pipeline Scenarios: A Comprehensive Approach to Supply Chain Management
Undersea pipelines for are a vital component of the global energy infrastructure, enabling the transportation of hydrocarbons from offshore production sites to onshore refineries and processing plants. These pipelines traverse vast distances across the ocean floor, enduring extreme pressure, harsh environmental conditions, and potential risks from marine life and equipment. Despite these challenges, undersea pipelines have become a critical lifeline for the energy industry, supporting the growing demand for across the globe. In this article, we will explore the design, construction, and operation of undersea pipelines for , including the key engineering challenges, safety considerations, and technological advancements that have shaped their evolution over the years.
Table of Contents
Undersea pipelines are an essential component
Undersea pipelines for are an essential component of the global energy infrastructure. These pipelines are used to transport from offshore production platforms or subsea wells to onshore processing plants or refineries. Undersea pipelines are typically made of high-strength steel, and are designed to withstand the harsh conditions of the ocean environment, including high pressure, corrosive saltwater, and powerful currents.
The construction of undersea pipelines is a complex and costly process that involves a number of engineering challenges. One of the biggest challenges is laying the pipeline on the seafloor. This is typically done using specialized vessels called pipe-layers, which lower the pipeline onto the seafloor using a combination of hydraulic and mechanical systems. The pipeline is then secured to the seafloor using specialized anchors and concrete weights to prevent it from shifting or moving.
Another challenge is ensuring the integrity of the pipeline over its lifetime. Undersea pipelines are subject to a number of potential hazards, including erosion, corrosion, and damage from underwater equipment or marine life. To address these risks, pipelines are typically coated with a layer of anti-corrosion material, and are regularly inspected using sophisticated equipment such as subsea robots or remotely-operated vehicles (ROVs).
In addition to construction and maintenance, undersea pipelines also require ongoing monitoring and control to ensure safe and efficient operation. This is typically done using a combination of sensors, meters, and other instrumentation that allow operators to monitor pipeline pressure, flow rate, temperature, and other critical parameters. In the event of a pipeline failure or leak, sophisticated control systems can quickly shut down the flow of oil or gas to prevent environmental damage.
Use
Undersea pipelines for play a critical role in meeting global energy demand, providing a safe and efficient means of transporting hydrocarbons from offshore production sites to onshore refineries and processing plants. Here are some of the key uses of undersea pipelines for :
- Offshore production: Many reserves are located beneath the ocean floor, requiring the use of offshore production platforms or subsea wells to extract the hydrocarbons. Undersea pipelines are used to transport the from these offshore facilities to onshore processing plants, where they can be refined into usable products such as gasoline, diesel fuel, and propane.
- Transport between countries: Undersea pipelines can also be used to transport between countries, providing a more efficient and cost-effective alternative to shipping. For example, the Nord Stream pipeline transports natural gas from Russia to Germany via the Baltic Sea, while the Trans-Mediterranean Pipeline transports natural gas from Algeria to Italy via the Mediterranean Sea.
- Distribution within countries: In some cases, undersea pipelines may also be used to transport within a country, particularly in areas where land-based transportation is difficult or impractical. For example, the Langeled pipeline in the North Sea transports natural gas from Norway to the United Kingdom, while the Peciko pipeline in Indonesia transports natural gas from offshore fields to onshore facilities.
Storage and transportation of liquefied natural gas (LNG): Undersea pipelines can also be used to transport liquefied natural gas (LNG), which is a compressed and cooled form of natural gas that is easier to transport and store than uncompressed natural gas. LNG is typically transported via specialized tankers to onshore terminals, where it is then transferred to undersea pipelines for transport to processing plants or distribution networks
Why ports use undersea pipelines
Ports may need undersea pipelines to supply ships with for a number of reasons. Here are some of the main reasons why ports may require undersea pipelines:
- Capacity: Ports that handle a high volume of shipping traffic may require large quantities of to fuel the ships that dock there. Undersea pipelines can provide a reliable and efficient means of delivering these fuels to the port, without the need for frequent deliveries by tanker trucks or other modes of transportation.
- Environmental considerations: In some cases, ports may be located in areas where strict environmental regulations prohibit the use of tanker trucks or other forms of transportation that could potentially pollute the surrounding waterways. Undersea pipelines provide a safe and environmentally-friendly means of delivering to the port.
- Cost-effectiveness: For ports located near offshore fields, it may be more cost-effective to transport the fuel via undersea pipelines rather than by tanker trucks or other modes of transportation. This can help to reduce transportation costs and improve the port’s overall profitability.
- Convenience: Undersea pipelines can provide a convenient and efficient means of delivering to ships at the port, without the need for additional storage facilities or complex delivery systems. This can help to streamline the delivery process and improve overall efficiency at the port.
In this project
- Our client was enquiring about the supply chain aspects of undersea pipelines.
- Setting up streamlined supply chain for undersea pipeline
- Whether to construct the port at given location or survey other locations
Analysis
How pipeline diameter, pipeline length, tank sizes, ships sizes and factory size affect under water pipeline for gas and oil?
Pipeline diameter, pipeline length, tank sizes, ship sizes, and factory size can all have significant impacts on the design, construction, and operation of undersea pipelines for gas and oil. Here’s how each of these factors can affect undersea pipelines:
- Pipeline diameter: The diameter of an undersea pipeline can have a significant impact on its capacity and efficiency. A larger diameter pipeline can transport more , but it may also be more expensive to construct and require more material. In addition, the pressure within the pipeline must be carefully monitored and controlled, which can be more challenging with larger diameter pipelines.
- Pipeline length: The length of an undersea pipeline can also affect its capacity and efficiency. Longer pipelines may require more pumping stations and other infrastructure to maintain pressure and ensure efficient transport of the . They may also be more susceptible to corrosion and damage over time.
- Tank sizes: The size of the tanks used to store prior to transportation can affect the overall efficiency of the pipeline system. Larger tanks may allow for more efficient transport of the fuel, reducing the need for frequent deliveries and improving the overall efficiency of the pipeline system.
- Ship sizes: The size of the ships used to transport can also have an impact on the design and operation of undersea pipelines. Larger ships may require larger pipelines to transport the fuel efficiently, while smaller ships may be more flexible but may require more frequent deliveries.
- Factory size: The size of the factories or processing plants that receive the transported by undersea pipelines can also impact the design and operation of the pipeline system. Larger factories may require larger pipelines to meet their fuel demands, while smaller factories may be able to operate with smaller pipelines.
The graph indicates that larger tank sizes require pipelines of longer length and larger diameter, which adds complexity and increases the cost of construction and maintenance. As the depth of water increases, additional drilling equipment and accessories become necessary, which further complicates the cost calculations. Moreover, complying with environmental regulations and obtaining clearance can be a significant overhead expense. Additionally, given that these pipelines may only be utilized for an average of 3-10 days per year, it raises concerns about the justification of the investment and its returns.
Undersea pipeline utilization
The number of utilization days for an undersea pipeline for oil and gas can vary depending on several factors, including the size of the pipeline, the volume of oil and gas being transported, and the demand for fuel at the receiving end of the pipeline.
In general, undersea pipelines for oil and gas are designed to operate continuously, with minimal downtime for maintenance and repairs. However, periodic maintenance and repairs are still necessary to ensure the safe and efficient operation of the pipeline. The frequency and duration of maintenance and repair activities can vary depending on the specific conditions and requirements of the pipeline.
For example, some pipelines may require more frequent maintenance and repairs if they are located in harsh environments or exposed to high levels of corrosion or wear. Other pipelines may require less frequent maintenance and repairs if they are constructed using high-quality materials and designed to withstand a wide range of environmental conditions.
In addition to periodic maintenance and repairs, the utilization days for an undersea pipeline may also be affected by fluctuations in demand for oil and gas at the receiving end of the pipeline. For example, if there is a significant decrease in demand for oil and gas, the pipeline may not need to operate at full capacity, resulting in lower utilization days.
Building streamline supply chain
Building a streamlined supply chain solution for a port with undersea pipelines involves several key steps. Here are some general guidelines for developing a streamlined supply chain solution:
- Conduct a comprehensive analysis of the port’s supply chain: This should include an assessment of the port’s existing infrastructure, including the undersea pipelines, tanks, ships, and processing facilities. It should also include an analysis of the demand for at the port, as well as any constraints or challenges that may be impacting the efficiency of the existing supply chain.
- Identify areas for improvement: Based on the analysis, identify areas where the supply chain can be streamlined to improve efficiency, reduce costs, and increase reliability. This may include optimizing the pipeline system, improving transportation logistics, or implementing new technologies to improve communication and coordination among stakeholders.
- Develop a plan for implementing changes: Once areas for improvement have been identified, develop a detailed plan for implementing changes to the supply chain. This may involve upgrading the existing infrastructure, implementing new technologies or processes, or collaborating with key stakeholders to improve communication and coordination.
- Monitor and measure performance: Once changes have been implemented, closely monitor and measure the performance of the supply chain to ensure that the changes are having the desired impact. This may involve implementing key performance indicators (KPIs) to track progress and identify areas where further improvements can be made.
Continuously improve the supply chain: Building a streamlined supply chain is an ongoing process that requires continuous improvement and adaptation. As the needs of the port evolve, be prepared to make further changes and improvements to the supply chain to ensure that it remains efficient, reliable, and cost-effective.
Recommendations
- After analysis, we recommended our client to not make their port at this location, and survey other properties.
- The construction of undersea pipelines is a costly endeavor, and in our client’s case, the limited utilization of the pipelines (only 3-10 days per year) raises concerns about the cost-effectiveness of the investment.
Key Learnings
- The construction and maintenance of undersea pipelines can be a costly and complex undertaking, requiring careful planning, engineering, and management.
- The diameter and length of the pipeline, as well as the tank and ship sizes, can significantly impact the performance and efficiency of the pipeline.
- Proper maintenance and monitoring of undersea pipelines are essential to ensure safe and efficient operation and prevent environmental damage.
- Undersea pipelines play a vital role in the energy supply chain, providing a cost-effective and reliable means of transporting oil and gas to markets around the world.
- By optimizing the use of undersea pipelines, ports can build a streamlined supply chain solution that ensures maximum uptime, reliability, and cost-effectiveness.
- The development of undersea pipelines should prioritize safety and environmental protection to ensure a sustainable energy infrastructure for future generations.
Conclusion
In conclusion, undersea pipelines for oil and gas play a critical role in the transportation of energy resources between ports and processing facilities. These pipelines provide a cost-effective, efficient, and reliable means of delivering oil and gas to markets around the world. However, the construction and maintenance of undersea pipelines can be a complex and costly undertaking, requiring careful planning, engineering, and management.
To optimize the use of undersea pipelines, it is essential to consider various factors such as pipeline diameter, pipeline length, tank sizes, ships sizes, and factory size. By taking into account these factors, ports can build a streamlined supply chain solution that ensures maximum uptime, reliability, and cost-effectiveness.
Moreover, undersea pipelines have to be designed and maintained to meet the highest safety standards to prevent environmental damage and protect human life. Continuous monitoring and maintenance are necessary to ensure the safe and efficient operation of these pipelines.
In summary, undersea pipelines for oil and gas are a vital component of the energy supply chain, providing an essential service that powers economies and improves the quality of life for millions of people around the world. By investing in the development of these pipelines and optimizing their use, we can create a more sustainable, efficient, and reliable energy infrastructure for future generations.
About the Author
Vivek Sood: Sydney based managing director of Global Supply Chain Group, a strategy consultancy specializing in supply chains. More information on Vivek is available on www.linkedin.com/in/vivek and more information on Global Supply Chain Group is available www.globalscgroup.com
Vivek is the Managing Director of Global Supply Chain Group, a boutique strategy consulting firm specialising in Supply Chain Strategies, and headquartered in Sydney, Australia . He has over 24 years of experience in strategic transformations and operational excellence within global supply chains. Prior to co-founding Global Supply Chain Group in January 2000, Vivek was a management consultant with top-tier strategy consulting firm Booz Allen & Hamilton.
Vivek provides strategic operations and supply chain advice to boards and senior management of global corporations, private equity groups and other stakeholders in a range of industries including FMCG, food, shipping, logistics, manufacturing, chemicals, mining, agribusiness, construction materials, explosives, airlines and electricity utilities.
Vivek has served world-wide corporations in nearly 500 small and large projects on all continents with a variety of clients in many different industries. Most of projects have involved diagnostic, conceptualisation and transformation of supply chains – releasing significant amount of value for the business. His project work in supply chain management has added cumulative value in excess of $500M incorporating projects in major supply chain infrastructure investment decisions, profitable growth driven by global supply chain realignment, supply chain systems, negotiations and all other aspects of global supply chains.
Vivek has written a number of path breaking articles and commentaries that are published in several respected journals and magazines. Vivek has spoken at several supply chain conference, forums and workshops in various parts of the world. He has also conducted several strategic workshops on various aspects of supply chain management. He received his MBA with Distinction from the Australian Graduate School of Management in 1996 and prior to these studies spent 11 years in the Merchant Navy, rising from a Cadet to Master Mariner.
More information on Vivek is available on www.linkedin.com/in/vivek and more information on Global Supply Chain Group is available on www.globalscgroup.com
Related Posts
Click below to see related posts.
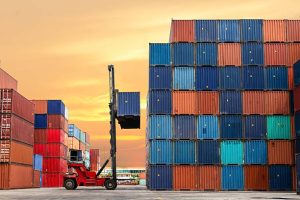
The Impact of Plummeting Shipping Container Prices Across Industries
Explore the far-reaching consequences of plummeting shipping container prices on diverse industries, revealing the intricate connections shaping global trade, supply chains, and economic landscapes.
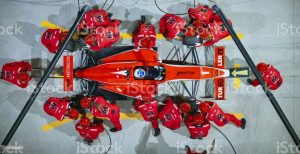
Race Day Logistics: Intricacies of Pit Stop
Explore the race day’s heartbeat: the art of pit stops. Uncover the intricate logistics orchestrating split-second tire changes, refuels, and strategy adjustments that define Formula 1’s high-speed drama.
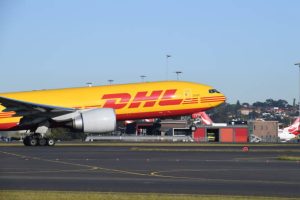
Mastering Travel Logistics in Formula 1 Racing
Discover the art of flawless travel logistics in the high-speed world of Formula 1. Uncover how precision planning and real-time coordination keep teams on track across the global circuit.